No, we don’t mean how much to tip that dude who just waxed your car. We mean knowing more about the stability factor of your industrial carts and trailers. A big consideration in the glamorous world of custom trailer design is determining the tipping factor of a load. It’s something our crack team of engineers figures out pretty early on in the design process.
There are several characteristics that come into play, all of which we plug into our handy dandy Tipometer—a magical spreadsheet that tells us whether or not a load passes on the stability front. Some factors to call out:
- Height and Center of Gravity: The higher the load’s center of gravity, the more likely it is to tip over during a high-speed turn. That’s because the forces that change a trailer’s path on a turn are all exerted at the bottom of the trailer. Typically, you want the load centered on the trailer, as well.
- The speed, RPM and Turning Radius are other important considerations. The faster and tighter the turn, the more those forces start to turn inwards.
- Slope: Even the slightest slope on the floor will impact your load’s tipping quotient.
- Torsional tip force: This tells us how much force is trying to tip the load over.
- Torsional stability force: This tells us how much force is trying to stabilize the load.
- Factor of Safety: For our trailer loads, we aim for a factor safety of 2—twice the standard. At the bare minimum, you want this number to be 100%. But at Hamilton, we aim for at least 200%.
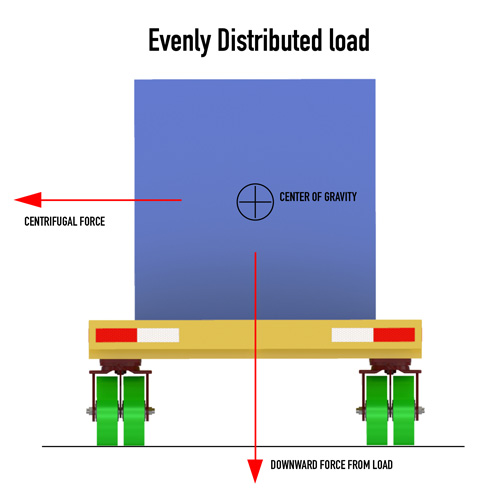
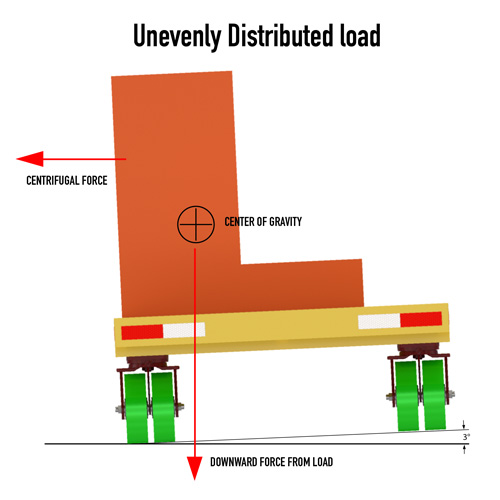
Now aren’t you feeling safer already?
To learn more about how load size, inclines, aisle width and environmental factors influence trailer design, download this Hamilton white paper.